A cool cabin comes at the expense of fuel, refrigerant, and the climate. My interviews with over 100 car mechanics in Southeast Asia suggest a straightforward solution.
It’s June in Malaysia, and air conditioners are cranked up high. Outside Ming Wah Car Cooler, a shop in Kuala Lumpur specializing in car air conditioning repair, there’s a line of cars waiting to be fixed. The drivers have their windows down and are wiping sweat off their foreheads.
Car air conditioning repair is a standalone business in Southeast Asia, where extraordinary heat and humidity result in an unusually high number of repair jobs. Unlike in the United States, where a car air conditioner might be repaired twice over the vehicle’s lifetime, cars in Southeast Asia commonly receive repairs on their air conditioners once every three years. So, it’s common to walk through a city and find entire districts – sometimes stretching several kilometers on end – packed with car air conditioning repair shops and parts suppliers.
Each year, car air conditioners account for 420 million tons of CO2e emissions, equivalent to the annual emissions of Mexico. Two-thirds of these emissions come from fuel consumption, with air conditioning accounting for 20 percent of a vehicle’s annual fuel consumption in hot climates. The other third comes from emissions of potent refrigerant gases such as hydrofluorocarbons (HFCs). And when you consider that refrigerant leakage can cause systems to consume more energy to perform the same function, that share may be even higher.
Car air conditioners emit refrigerant in two ways. First, car air conditioners are prone to refrigerant leaks. Unlike their stationary counterparts, mobile air conditioning systems aren’t hermetically sealed at the factory. Instead of soldered, leak-tight connections, car air conditioning systems are held together with an array of nuts and bolts. After thousands of kilometers of driving, bumps, and vibration, these connections loosen, invariably leading to refrigerant leaks. Leaks have several deleterious effects: the air conditioner becomes less energy efficient, parts like the compressor wear down faster, and your car stops blowing cold air.
Second, when car mechanics need to repair major components of the system, they first need to empty out any residual refrigerant gas. They can use specialized equipment to suck out the refrigerant, and following repairs, pump the same gas back in. This equipment pays off for the mechanic and the planet. By reusing the gas, mechanics don’t have to buy as much new gas and emit less refrigerant into the atmosphere.
But if mechanics don’t own the equipment – which can cost several thousands of dollars, or half a year’s salary – they must release the gas into the air. Because refrigerants are so potent, releasing the 400-some grams of refrigerant in a typical system has the same impact on the climate as emitting hundreds of kilograms of CO2.
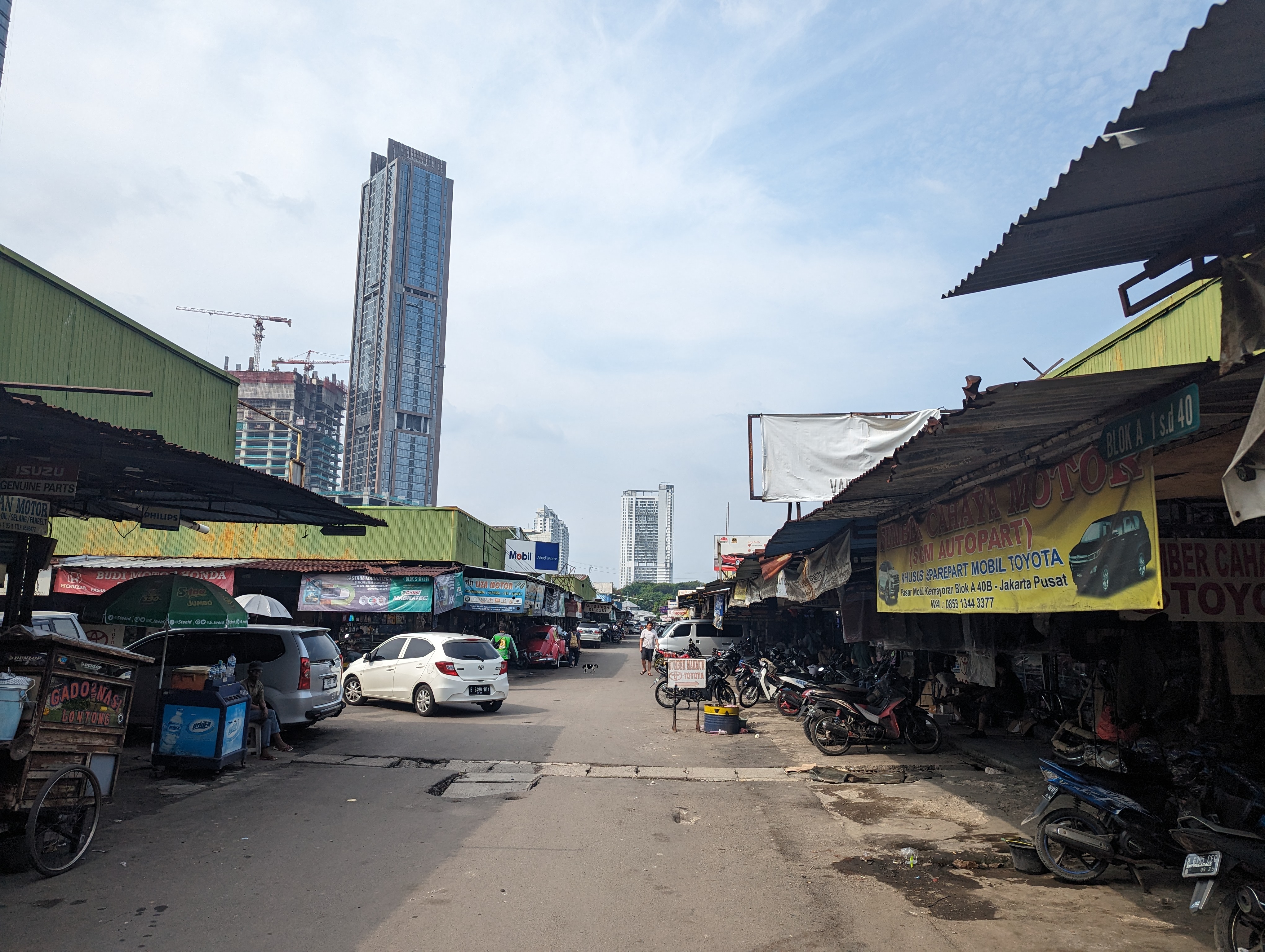
Many car manufacturers, especially in Europe and the United States, have started to use a new chemical called HFO-1234yf, which has minimal impact on climate, in their air conditioners. But most mechanics in Southeast Asia have never heard of HFO-1234yf, in part because Western cars are rare and domestic manufacturers haven’t yet made the switch to HFOs. Furthermore, HFCs – despite being ultra-potent greenhouse gases – are commonly believed to be environmentally friendly. Unlike their chlorofluorocarbon (CFC) predecessors, HFCs do not deplete the ozone layer.
As a result, in the rare instance when a car using HFOs does come in for repairs, mechanics often service the air conditioning system with HFCs. This practice reduces the climate benefit of the system’s original design.
This practice arises because of inadequate training about the climate effects of HFCs, but also from the economics of air conditioning servicing. Mechanics – especially in bustling repair districts – are eager to cut costs to remain competitive. Purchasing HFOs – which are currently at least 12 times more expensive than HFCs per kilogram – and buying separate HFO servicing equipment could drive a mechanic out of business, even if it means doing the right thing for the climate.
Of course, the solution to these challenges in the servicing sector isn’t to do away with car air conditioning, nor to guilt-trip drivers and passengers into enduring the blistering heat. Instead, there’s a straightforward solution: to give mechanics free equipment and training to reduce the climate impact of their servicing practices.
Indeed, some countries – supported by the United Nations Multilateral Fund – have done it before. In the 1990s and 2000s, at the beginning of the CFC phaseout, countries such as Malaysia and Indonesia gave out hundreds of free refrigerant recovery machines to car mechanics. These countries also educated technicians about the environmental impact of CFC emissions, which at the time were driving both climate change and ozone depletion. These programs helped the CFC phaseout become a massive success in the motor vehicle sector, with refrigerant emissions declining precipitously even as the number of cars on the road increased.
These programs also have had enduring climate benefits, even after the CFC phaseout. Many mechanics who currently use recovery equipment do so because they enjoyed using their first free machine so much. These mechanics who use machines often teach their trainees how to use machines, too, which results in the proliferation of good servicing practices when trainees eventually leave to start their own shops.
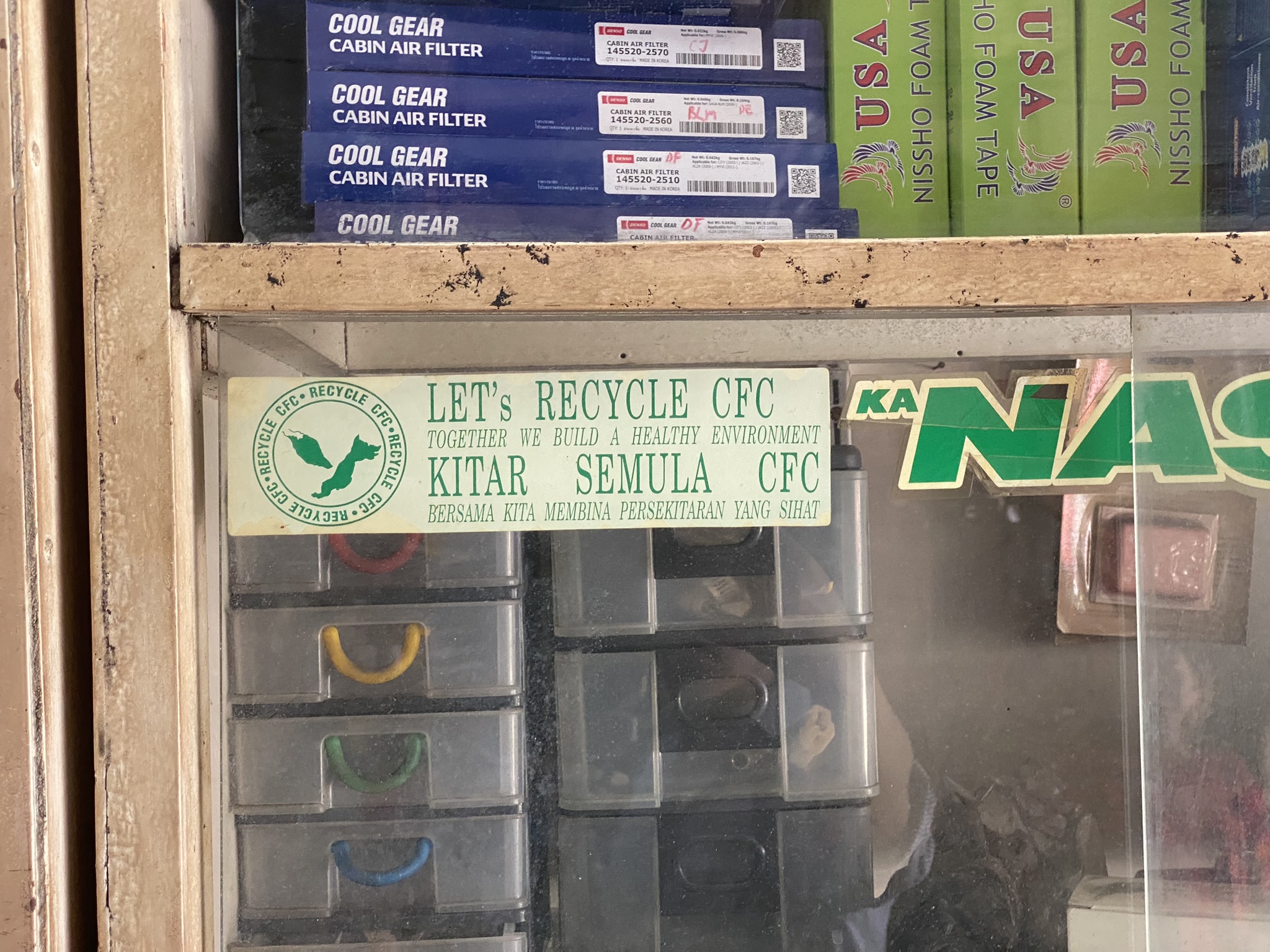
But today, training and technology are behind the times. Most free machines have broken and are collecting dust in the corner of repair shops. Not all mechanics have the money to replace them.
And even though the mechanics I interviewed disagreed with each other about some things, like the best brand of refrigerant, they all agreed about one thing: if they had the money to buy a recovery machine, they would certainly be using one.
Training for technicians to recover HFCs and learn how to repair air conditioners containing HFOs is long overdue. Beyond environmental impact, trainings should also emphasize how appropriate recovery equipment can have direct benefits for the technician: making repair jobs easier, saving money for the business and the customer, and making air conditioners blow colder air. In the repair industry, where most mechanics begin their careers by learning from friends and family, good training can lead to generational knowledge.
This week, delegates to the Montreal Protocol are in Bangkok deciding how to replenish and appropriate the next triennium of the Multilateral Fund. It’s critical that the mobile sector isn’t left out of appropriations, especially as HFO-1234yf just begins to enter the market in the developing world.
There’s a saying in the car industry that customers are happy to pay for repairs for only one thing in their car – and that’s the air conditioning. In the climate world, we should be happy to pay, once again, for the equipment and training for technicians to reduce emissions from HFCs. It’s a simple solution, but it’s worked before, and it can work again.
Special thanks to our colleagues, Kristen Taddonio and Steve Schaeber (Mobile Air Climate Systems Association), and the World Bank for providing the financial and technical support for this project. I’m also very grateful to Andi Junila Aulia and Jessica Ng Wai Kwan for their skillful translation in interviews with car mechanics.
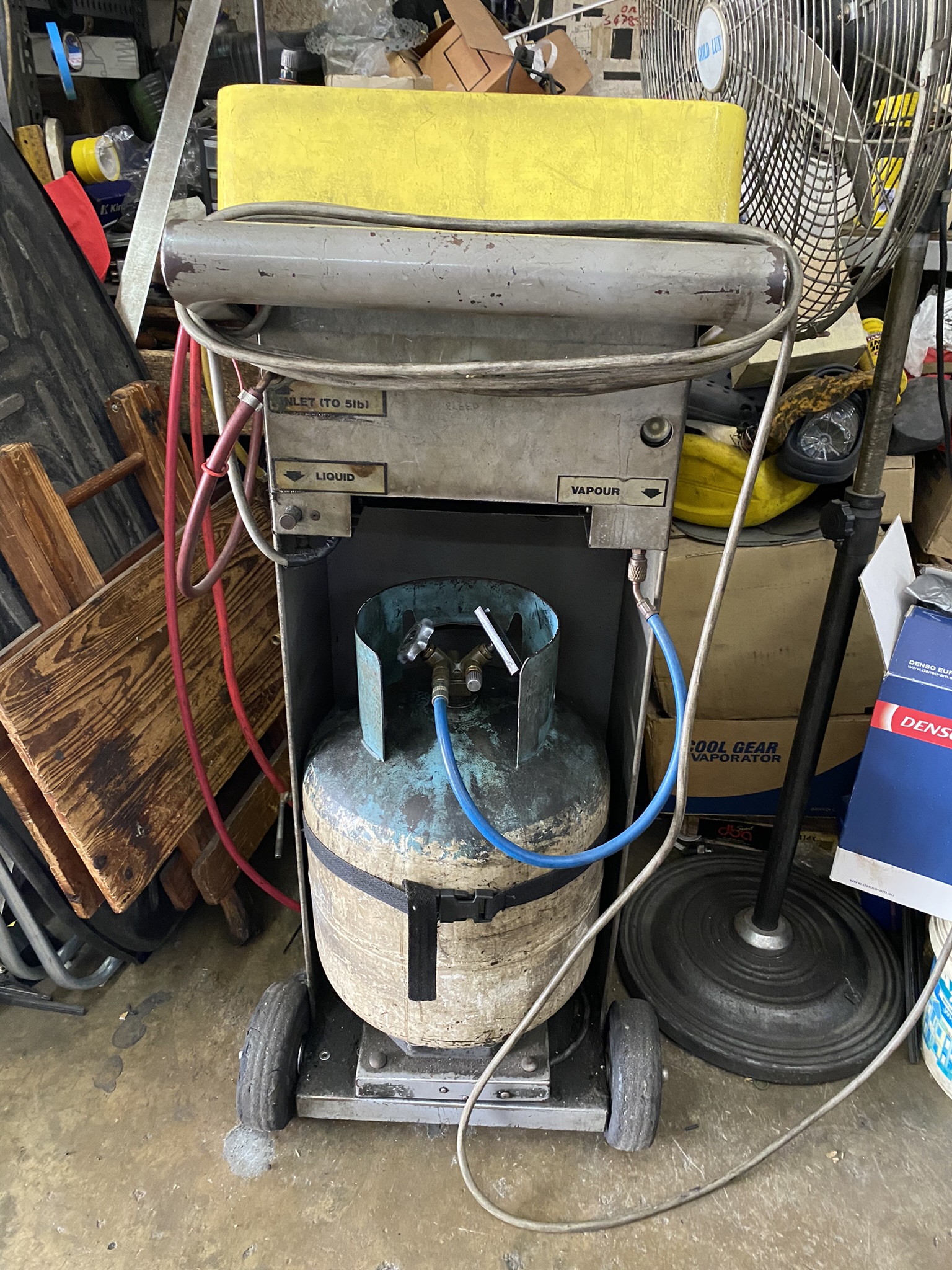
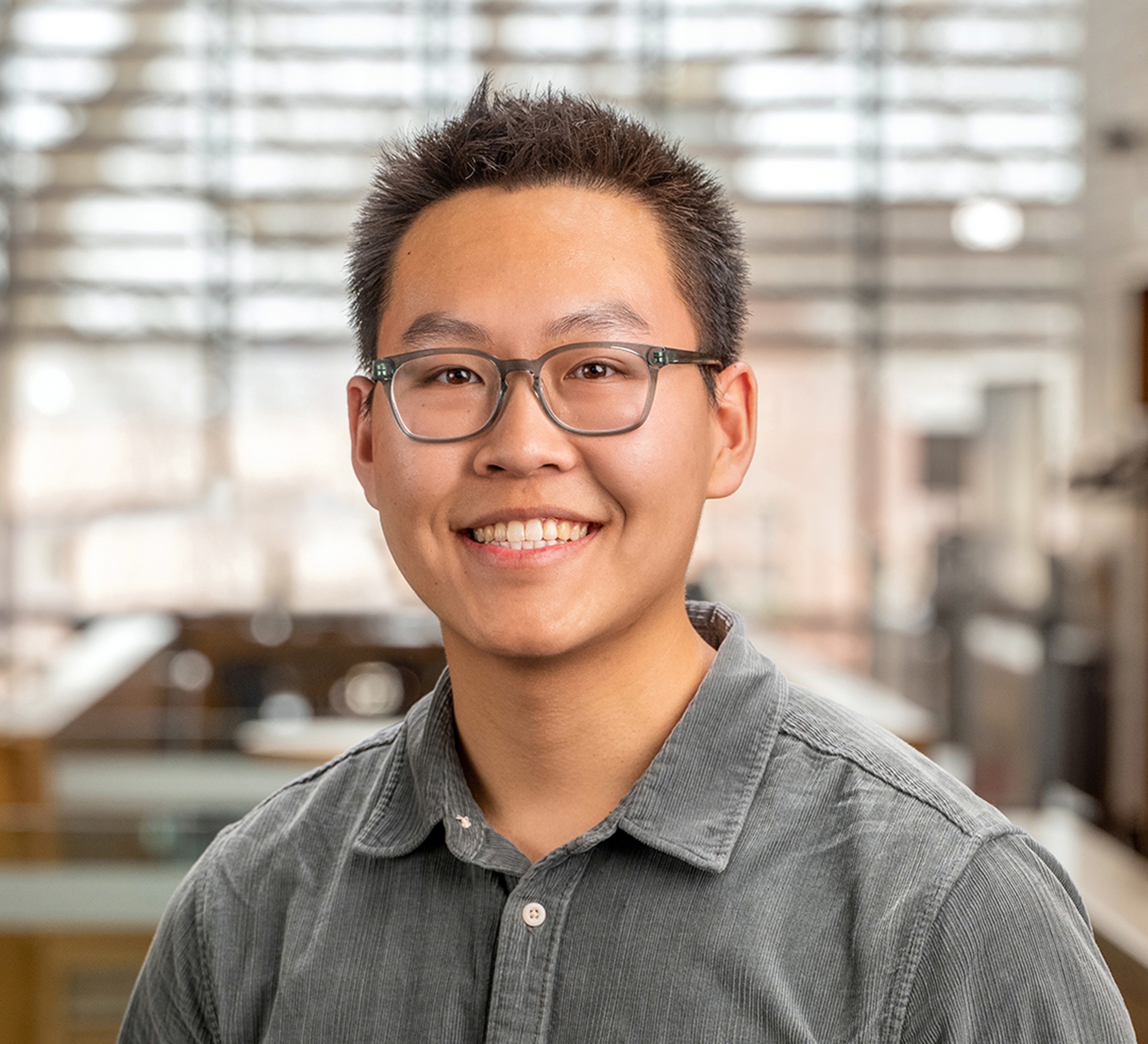